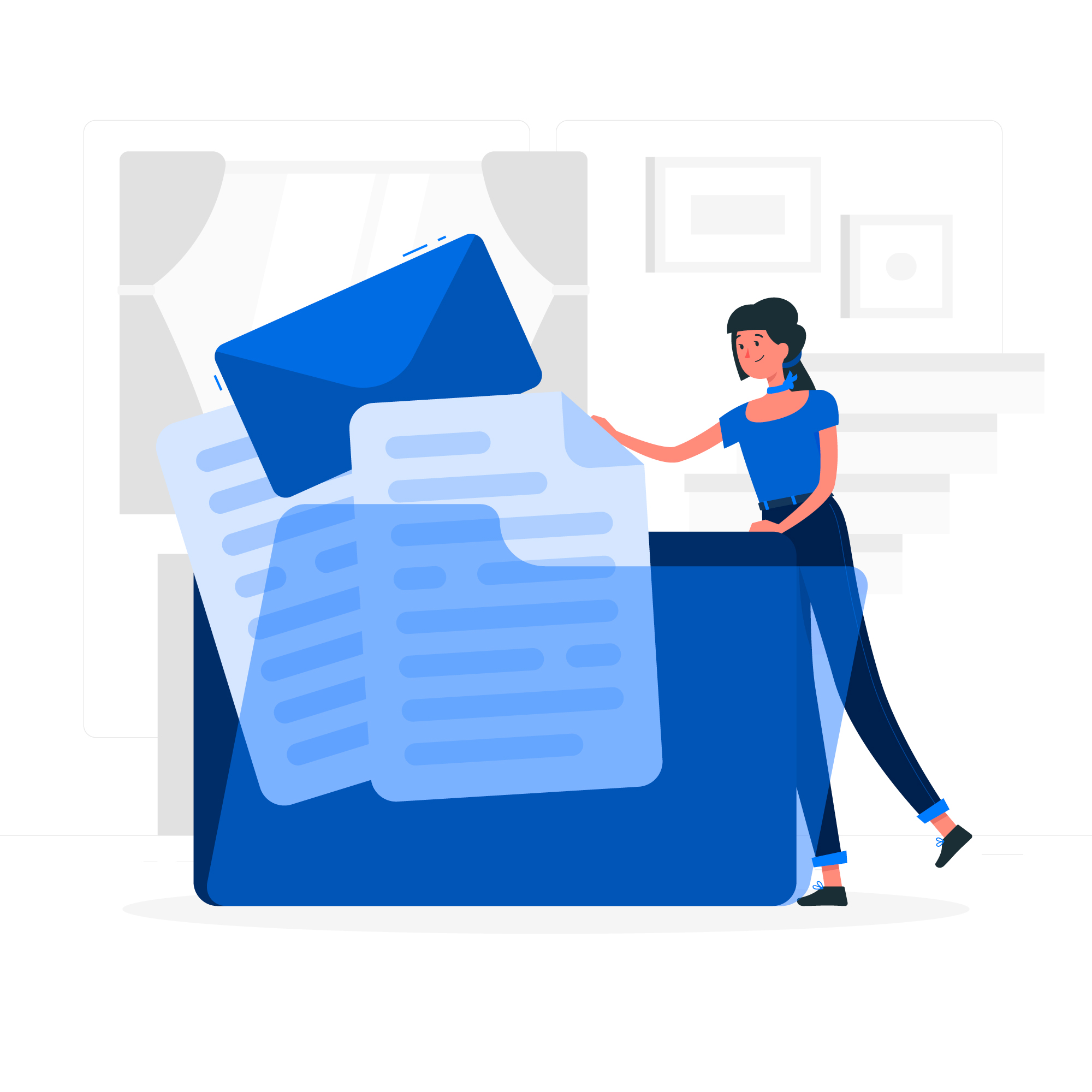
Unplanned equipment failures are a facility manager’s worst nightmare. These failures can disrupt daily operations, lead to unanticipated downtime, and result in costly repairs or even complete shutdowns. Such issues not only affect productivity but can also impact the bottom line, customer satisfaction, and employee safety. To effectively handle unplanned equipment failures, facility managers must have robust strategies in place. One such strategy involves leveraging a comprehensive Business Process Management (BPM) solution like Sweven BPM.
The Impact of Unplanned Equipment Failures
Unplanned equipment failures can cause a ripple effect throughout a facility’s operations. Here’s how:
- Operational Downtime: When a critical piece of equipment fails unexpectedly, it can halt entire processes, leading to significant downtime. This downtime can disrupt production schedules, delay service delivery, and result in unmet deadlines.
- High Repair Costs: Unplanned failures often require urgent repairs, which tend to be more expensive than planned maintenance. Emergency repair services, rush orders for parts, and overtime for maintenance staff can quickly add up.
- Loss of Productivity: Equipment failures mean that teams are unable to complete their tasks on time. This loss of productivity can affect overall facility performance, reduce employee morale, and increase the risk of missed business opportunities.
- Safety Risks: Equipment failures can create hazardous conditions for employees and visitors. For example, a malfunctioning HVAC system could lead to temperature extremes, while a failed conveyor belt could cause accidents or injuries.
- Decreased Asset Lifespan: Frequent breakdowns can reduce the lifespan of equipment. Unplanned failures can cause significant damage, resulting in more frequent replacements and higher capital expenditures over time.
Strategies for Managing Unplanned Equipment Failures
To mitigate these risks, facility managers need to adopt proactive strategies. Here are some key approaches:
- Implement Preventive Maintenance: Regularly scheduled maintenance is crucial to prevent equipment from reaching a point of failure. Facility managers should create a maintenance schedule that aligns with manufacturer recommendations and operational requirements.
- Conduct Root Cause Analysis: When equipment fails, it’s essential to identify the root cause of the failure. This analysis helps in understanding why the failure occurred and in implementing measures to prevent future occurrences.
- Develop Emergency Response Plans: Facility managers should have well-documented plans for responding to equipment failures. This includes a clear chain of command, pre-approved vendors for emergency repairs, and readily available replacement parts.
- Utilize Data for Predictive Maintenance: Predictive maintenance uses data from sensors, historical records, and other sources to predict when equipment is likely to fail. This allows for maintenance to be performed just in time to prevent failure.
- Leverage Technology: Modern facilities can benefit from digital tools and software that provide real-time monitoring, automated alerts, and centralized data management. This is where Sweven BPM can make a significant impact.
How Sweven BPM Can Help Handle Unplanned Equipment Failures
Sweven BPM offers a powerful suite of tools specifically designed to help facility managers manage unplanned equipment failures more effectively. Here’s how it can help:
- Automated Preventive Maintenance Scheduling: Sweven BPM allows facility managers to automate preventive maintenance schedules, ensuring that all equipment is serviced regularly and on time. Automated notifications and reminders can be set up to alert the maintenance team about upcoming tasks, reducing the chances of missed maintenance activities.
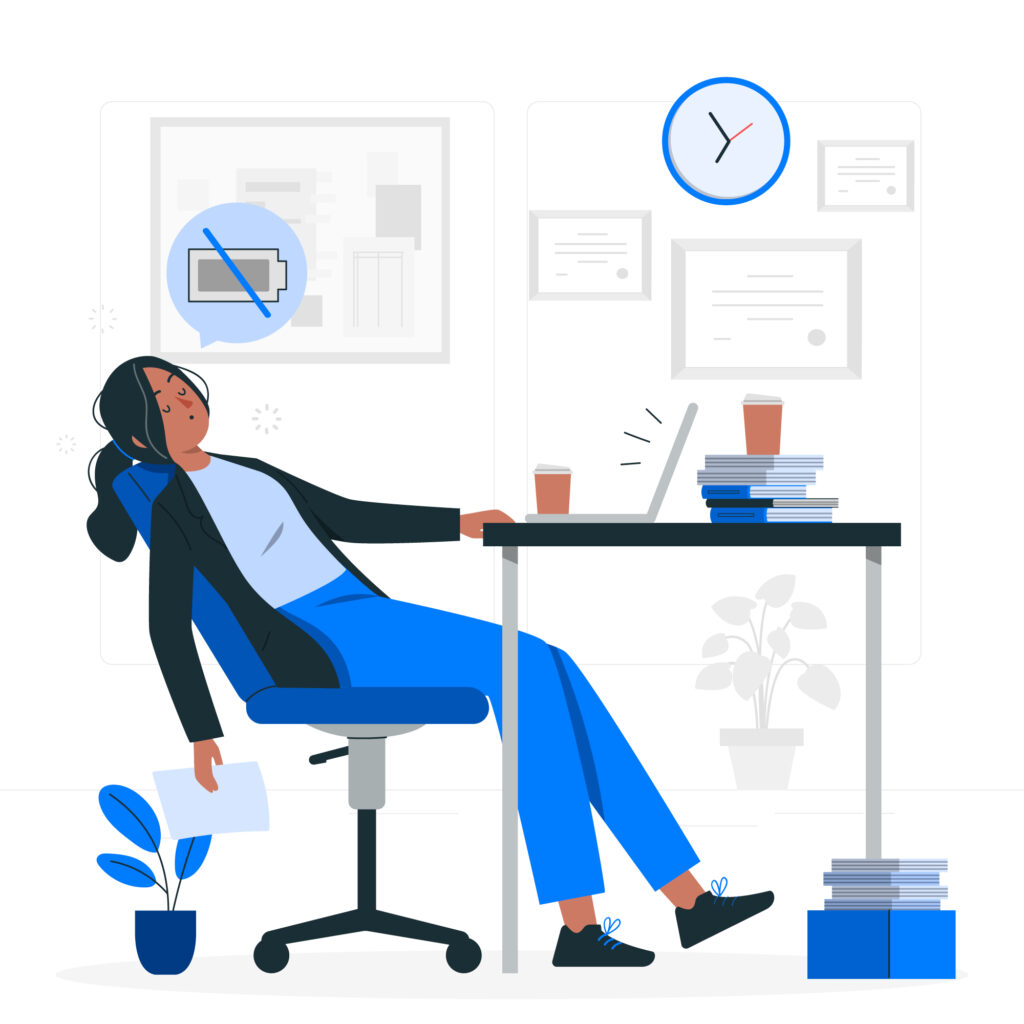
- Centralized Incident Management: When equipment fails, swift action is crucial. Sweven BPM provides a centralized platform where all incidents can be reported, tracked, and managed in real time. This streamlines communication between maintenance teams, managers, and vendors, ensuring quick resolution of issues.
- Real-Time Monitoring and Alerts: Sweven BPM integrates with IoT devices and sensors to provide real-time monitoring of equipment health. It can automatically trigger alerts when specific thresholds are breached, enabling facility managers to act before a minor issue becomes a major problem.
- Root Cause Analysis and Reporting: With Sweven BPM, facility managers can easily conduct root cause analyses by accessing historical data, maintenance records, and incident reports. The platform provides detailed analytics and reporting features, helping managers identify patterns and implement corrective measures.
- Efficient Resource Management: Sweven BPM helps facility managers allocate resources more effectively by providing a clear overview of all tasks, personnel, and equipment. This makes it easier to assign the right team to handle an unplanned failure and ensures that the necessary resources are available when needed.
- Improved Vendor Coordination: Sweven BPM streamlines the coordination with third-party vendors by maintaining a database of approved vendors, service contracts, and contact information. When an unplanned failure occurs, the platform can automatically notify vendors and track their response time and performance.
Key Benefits of Using Sweven BPM for Managing Equipment Failures
By implementing Sweven BPM, facility managers can experience several benefits that help mitigate the impact of unplanned equipment failures:
- Reduced Downtime: Real-time monitoring, automated alerts, and swift incident management reduce the time it takes to identify and resolve equipment failures, minimizing downtime.
- Lower Repair Costs: Automated preventive maintenance and predictive insights help avoid costly emergency repairs by catching issues early and preventing failures.
- Increased Equipment Lifespan: Regular maintenance and timely repairs reduce the wear and tear on equipment, extending its lifespan and reducing the need for replacements.
- Enhanced Safety: Quickly identifying and resolving equipment failures reduces the risk of accidents and injuries, ensuring a safer environment for employees and visitors.
- Data-Driven Decision-Making: Sweven BPM’s analytics and reporting tools provide valuable insights that help facility managers make informed decisions about maintenance schedules, equipment investments, and resource allocation.
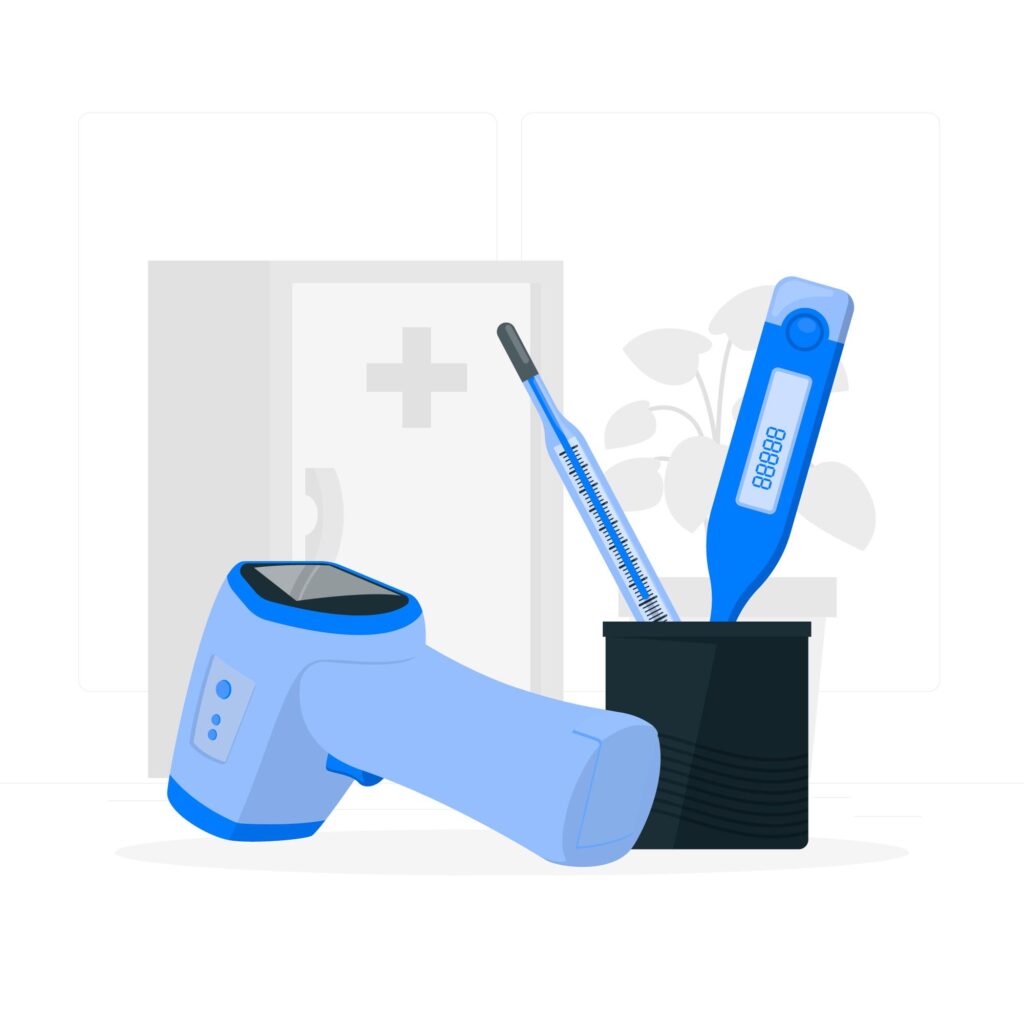
Conclusion
Unplanned equipment failures are inevitable, but their impact doesn’t have to be catastrophic. By adopting proactive strategies and leveraging powerful tools like Sweven BPM, facility managers can minimize downtime, reduce costs, and enhance overall operational efficiency. Sweven BPM’s comprehensive suite of features provides the visibility, automation, and data insights needed to effectively manage equipment failures, ensuring smooth and uninterrupted operations.
If you’re a facility manager looking to handle unplanned equipment failures with greater confidence and control, consider integrating Sweven BPM into your facility management strategy. Take the first step toward reducing downtime, lowering costs, and keeping your facility running like a well-oiled machine.