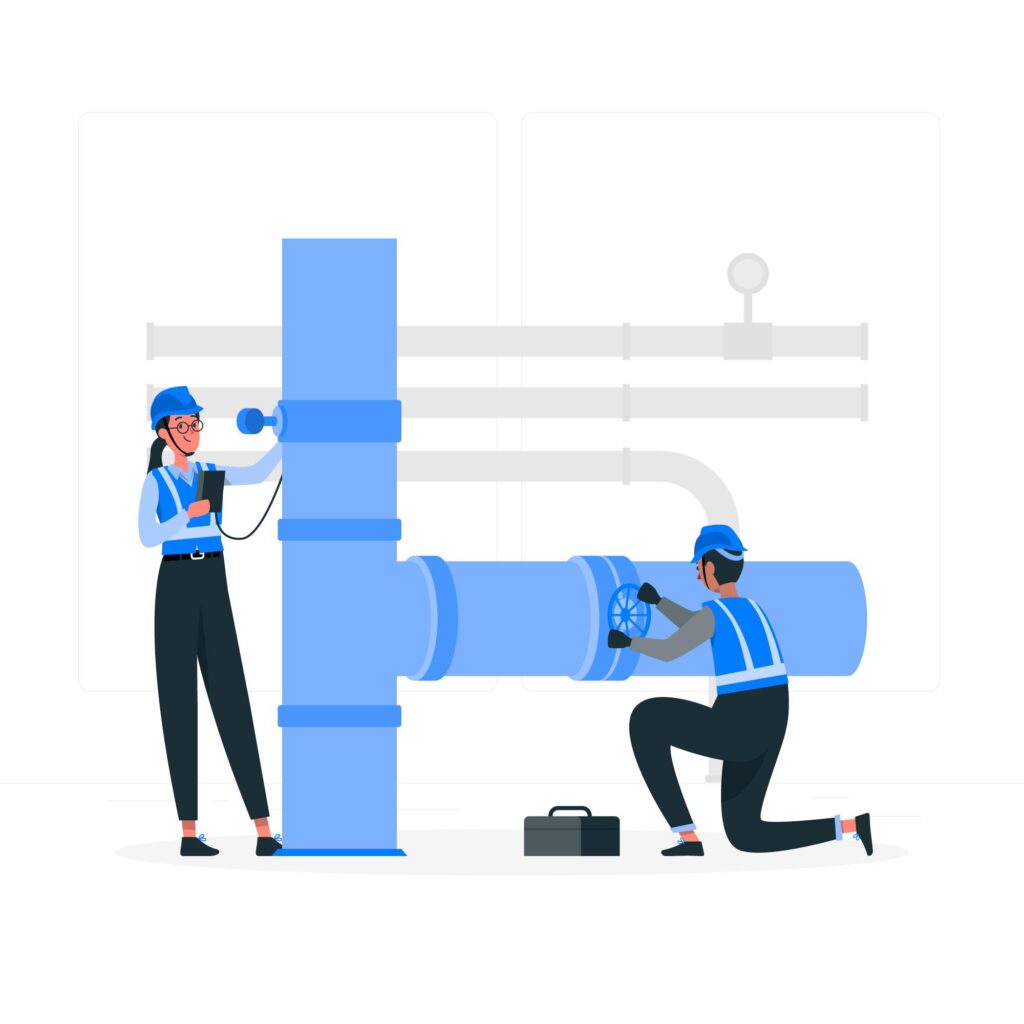
Facilities maintenance is a critical function that ensures the smooth operation of buildings and equipment. However, many organizations face a significant challenge: a shortage of skilled maintenance workers. This shortage can lead to delayed maintenance work and subpar service quality, impacting overall efficiency and productivity. Sweven offers solutions to address these challenges by investing in training and development programs, offering competitive compensation and benefits, and utilizing automation and technology to supplement the workforce and improve efficiency.
Pain Point: Shortage of Skilled Maintenance Workers
Workforce shortages in facilities maintenance can create several issues:
- Delayed Maintenance: With fewer skilled workers available, maintenance tasks are often delayed, leading to increased downtime and potential disruptions.
- Subpar Work Quality: A lack of skilled personnel can result in maintenance work that does not meet the necessary standards, causing recurring issues and inefficiencies.
Increased Workload: Existing workers may face an overwhelming workload, leading to burnout and decreased job satisfaction.
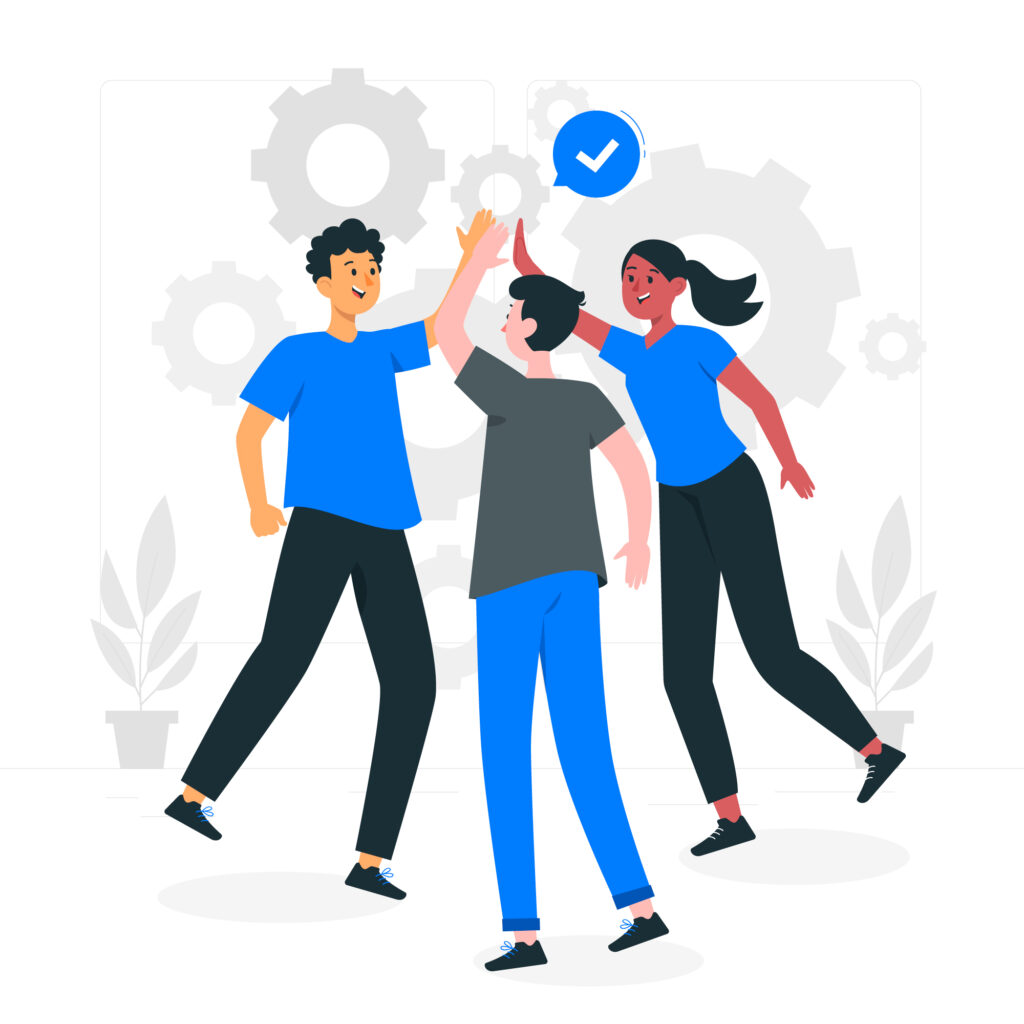
Solution: Comprehensive Strategies to Address Workforce Shortages
Sweven provides a multifaceted approach to overcoming workforce shortages in facilities maintenance:
- Training and Development Programs: Investing in comprehensive training and development programs is crucial for building a skilled workforce. Sweven can help organizations design and implement training initiatives that enhance the skills of existing employees and prepare new hires for the demands of facilities maintenance. By fostering continuous learning and professional growth, organizations can develop a more capable and resilient workforce.
- Competitive Compensation and Benefits: Offering competitive compensation packages and benefits is essential for attracting and retaining skilled maintenance workers. Sweven provides insights into industry standards and helps organizations structure attractive compensation plans that include not only salary but also benefits such as health insurance, retirement plans, and opportunities for career advancement. This approach can significantly reduce turnover and build a more stable workforce.
- Utilizing Automation and Technology: Sweven leverages advanced automation and technology to supplement the workforce and improve efficiency. By implementing automated systems for routine maintenance tasks, organizations can free up skilled workers to focus on more complex and critical issues. Additionally, Sweven’s data analytics tools can help predict maintenance needs and optimize task scheduling, ensuring that the available workforce is used effectively.
- Enhanced Efficiency Through Technology: Sweven’s technology platform includes features that enhance overall efficiency, such as real-time monitoring, predictive maintenance, and streamlined communication channels. These tools enable maintenance teams to work more efficiently and effectively, reducing the impact of workforce shortages.
Outsourcing and Partnerships: When internal resources are insufficient, Sweven can assist organizations in identifying reliable outsourcing partners. By forming strategic partnerships, organizations can ensure that maintenance needs are met without compromising quality or efficiency.
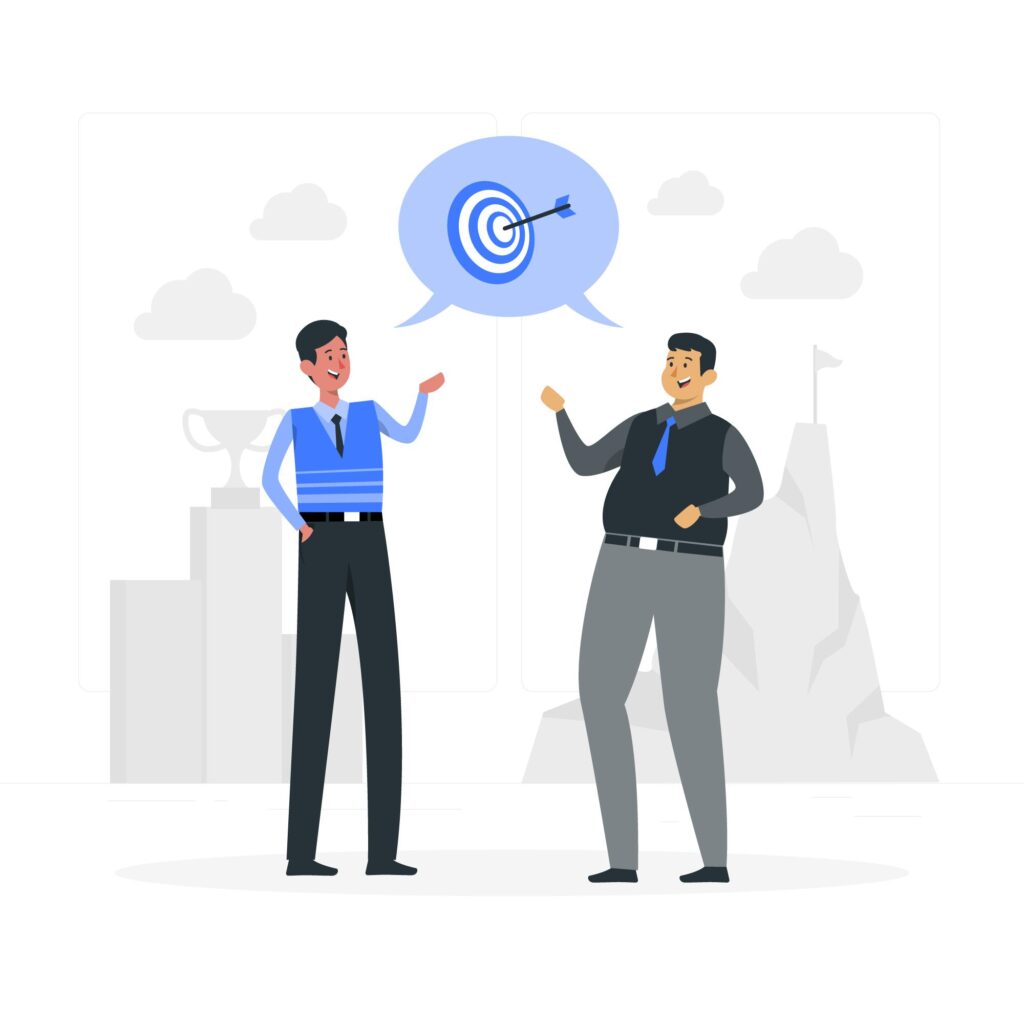
Conclusion
Workforce shortages in facilities maintenance present a significant challenge, but they are not insurmountable. Sweven offers a comprehensive solution by investing in training and development programs, offering competitive compensation and benefits, and utilizing automation and technology to supplement the workforce. By adopting these strategies, organizations can mitigate the impact of workforce shortages, ensuring timely and high-quality maintenance work. Sweven’s holistic approach not only addresses immediate staffing challenges but also builds a more robust and capable maintenance workforce for the future.